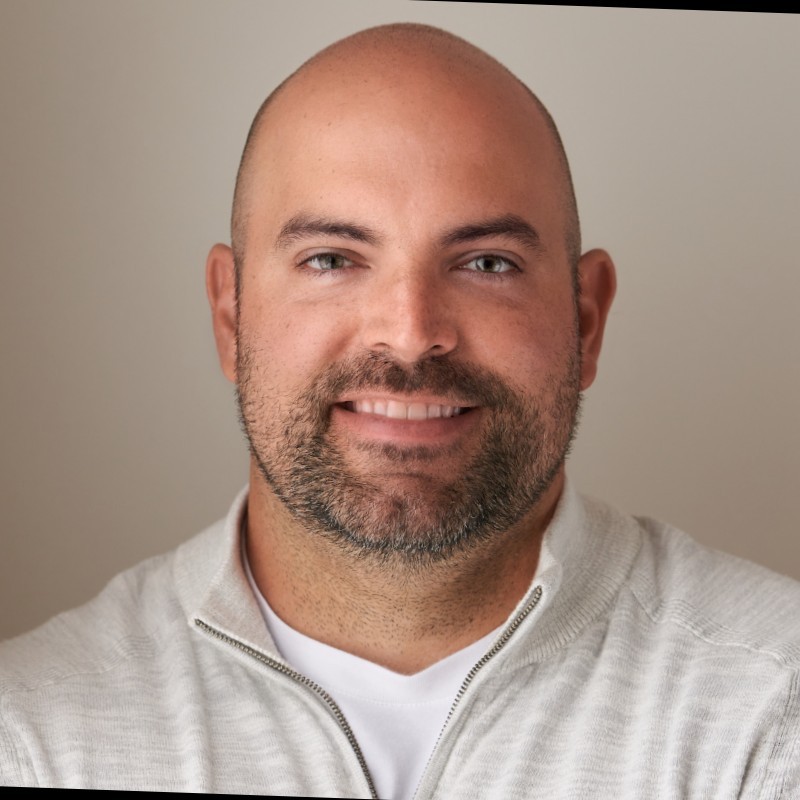
Understand control deficiency remediation, its importance, and how to effectively identify and address weaknesses in your security controls for a stronger business.
Running a business is like navigating a ship through unpredictable waters. You need a reliable navigation system and a sturdy hull to weather any storm. In the financial world, your internal controls are that navigation system and hull. Control deficiency remediation is the ongoing maintenance that keeps them in top shape. This guide provides a practical roadmap for identifying, assessing, and addressing weaknesses in your controls. We'll cover everything from understanding different types of deficiencies to developing a remediation plan and leveraging technology for automation. Whether you're a seasoned financial professional or just starting out, this guide will equip you with the knowledge and tools to strengthen your financial defenses and steer your business toward success.
Control deficiency remediation is how you identify, assess, and address weaknesses in your security controls. Think of it as patching holes in your company's defenses to make it more resilient. This isn't a one-time fix, but an ongoing process of strengthening your systems and processes.
Remediation is crucial for maintaining the effectiveness of your internal control system. A strong internal control system protects your assets, ensures accurate financial reporting, and helps you comply with regulations. Without regular checks and remediation, these controls can weaken, leaving your company vulnerable. A structured remediation process helps you stay on top of potential issues and address them proactively. This, in turn, allows you to maintain accurate financial records and make informed business decisions.
Effective remediation requires company-wide collaboration. Getting everyone on board helps implement the fixes and builds a culture of compliance. When everyone understands the importance of strong controls, it becomes ingrained in how your company operates. By systematically addressing control deficiencies, you can mitigate risks and improve your overall governance and risk management. This proactive approach also helps address compliance gaps and builds a stronger, more resilient organization. Ultimately, effective control deficiency remediation contributes to a more secure and successful business.
Spotting weaknesses in your internal controls is the first step toward stronger financial reporting and smoother audits. Let's break down how to identify these control deficiencies.
A design deficiency exists when a control is either missing entirely or isn't set up in a way that can actually catch errors. Think of it like a security system with no cameras—it's not going to be very effective. For example, if your process for approving invoices lacks a step for verifying quantities received, that's a design flaw. Without that check, you could be paying for goods you never actually got. The Public Company Accounting Oversight Board (PCAOB) offers further guidance on control deficiencies in their Auditing Standard No. 325.
An operational deficiency happens when a control exists but isn't working as intended. This could be due to a few reasons: maybe the process isn't being followed consistently, or perhaps the people carrying it out aren't adequately trained. Imagine you do have a process for verifying invoice quantities, but your team is overwhelmed and sometimes skips it. That's an operational deficiency. Or, if the person responsible for the check doesn't understand the inventory system, they might miss discrepancies. For more information, refer to the PCAOB's Auditing Standard No. 325.
Control deficiencies, whether design-related or operational, can create a ripple effect of problems, from financial losses to legal headaches. Reputational damage can also result from control deficiencies. To effectively evaluate your internal controls, focus on these five key areas:
After identifying potential control deficiencies, the next step is evaluating their severity and potential impact. This involves a thorough assessment to understand the risks associated with each deficiency and prioritize remediation efforts.
Start by clearly identifying the deficiency. Determine what exactly went wrong, when it occurred, and who was involved. For example, if you discover a recurring error in your sales order processing, pinpoint the specific step in the process where the error originates. This initial step is crucial for understanding the scope of the problem and its potential consequences. Knowing the “who, what, when, and where” of the deficiency helps you isolate the issue and prevents it from being misinterpreted or minimized.
Once you've identified the weakness, consider the potential impact. Ask yourself: How likely is this error to recur? What are the potential financial or operational consequences if it does? A small error with a high likelihood of recurrence might be more critical than a large, improbable error. For instance, a minor error in pricing that occurs frequently could significantly impact revenue over time. Conversely, a one-time, large error, while serious, might not pose the same ongoing risk. This assessment helps you prioritize which deficiencies need immediate attention. Evaluating internal control deficiencies requires careful consideration of both the likelihood and the magnitude of potential problems.
Don't just treat the symptoms—address the root cause. Dig deeper to understand why the control failed. Was it due to a lack of training, inadequate procedures, or a system flaw? Analyzing the root cause is essential for developing effective solutions and preventing recurrence. For example, if employees consistently make errors because they haven't received proper training, simply correcting the errors won't prevent them from happening again. Investing in training addresses the root cause and strengthens the control environment.
Finally, thoroughly document your findings. This includes a description of the deficiency, its potential impact, the root cause analysis, and any recommended corrective actions. Documenting your conclusions creates a record of your assessment process and provides valuable insights for future evaluations and audits. Clear documentation also promotes transparency and accountability within the organization. This documentation will be essential when developing and implementing your remediation plan.
Once you’ve identified and evaluated control deficiencies, it’s time to fix them. This involves developing a remediation plan, implementing corrective actions, and monitoring the results. A structured approach is key to successful remediation.
Start by creating a detailed remediation plan. This plan should outline the specific steps needed to address each deficiency. Think of it as a roadmap for fixing your control issues. A clear governance framework, defining roles and responsibilities, is essential for effective controls remediation planning. Make sure you involve key stakeholders in this process to ensure buy-in and collaboration. Successful remediation relies on careful planning and stakeholder engagement.
With a plan in place, you can begin implementing corrective actions. This might involve revising procedures, strengthening oversight, providing additional training, or implementing new technologies. Responding to control deficiencies with a structured process is crucial for maintaining the integrity of your internal control system. Resources on testing and monitoring controls emphasize this importance. Proactively identifying and remediating control gaps strengthens your overall control environment.
Remediation isn’t a one-time fix. Continuous monitoring is crucial to ensure the effectiveness of your corrective actions. Establish specific, measurable, achievable, relevant, and time-bound (SMART) metrics and key performance indicators (KPIs) to track your progress. Regularly review the results and make adjustments as needed. Tracking trends by risk criticality and measuring team performance over time helps improve overall operations. Consider exploring resources on monitoring security remediation for further insights. This ongoing monitoring helps ensure that the control deficiencies are truly resolved and prevents them from recurring.
Remediating control deficiencies isn't always a walk in the park. It often requires a shift in mindset, resources, and processes. Let's explore some common challenges and how to address them.
One of the biggest hurdles in remediation is limited resources. Teams often juggle multiple priorities, and dedicating the necessary time and staff to remediation can be tough. This can lead to rushed efforts and incomplete fixes. To counter this, prioritize remediation activities based on risk. Focus on the most critical deficiencies first and allocate resources accordingly. Consider using project management tools to track progress and ensure accountability. If internal resources are truly stretched thin, explore bringing in outside experts to help with the process. Sometimes, a fresh perspective can bring valuable insights and speed things up. For more insights on resource allocation, see this article on the value of proper internal control remediation.
People naturally resist change. Implementing new controls or processes can be met with pushback. Clearly communicate the reasons for the changes and the benefits they'll bring. Involve staff in the remediation process to create a sense of ownership. Training is essential. Make sure everyone understands the new controls and how they fit into the bigger picture. Consider different training approaches to accommodate different learning styles. Regular communication and feedback can help address concerns and smooth the transition. This article on remediation guidance offers helpful advice on managing change during the remediation process.
Many organizations have intricate systems and processes, making it difficult to pinpoint the root cause of control deficiencies. A thorough analysis is essential. Don't just treat the symptoms; understand the underlying issues. This might involve reviewing process documentation, interviewing staff, and analyzing data. Remember that a single root cause can impact multiple areas, so a holistic approach is key. This resource on remediation and restatement provides a framework for identifying and addressing root causes.
Remediation efforts shouldn't disrupt day-to-day operations. Find a balance between fixing control deficiencies and keeping the business running smoothly. Phased implementation can be helpful. Start with smaller, less disruptive changes and gradually introduce more complex ones. Maintain open communication with stakeholders to manage expectations and minimize disruptions. Consider working with experts who specialize in internal control remediation to ensure a seamless integration of remediation efforts with ongoing operations.
Once you’ve identified and assessed your control deficiencies, it’s time to implement solutions. These best practices will help you remediate effectively and efficiently.
Successful remediation relies on collaboration. Get key people involved early, from department heads to IT staff to external auditors. Clear communication and defined roles are essential. This ensures everyone understands their responsibilities and how their work contributes to the overall remediation effort. When you effectively allocate resources and set realistic timelines, you set your team up for success. Open communication channels also help address roadblocks proactively.
Your team needs the right knowledge to maintain strong controls. Regular training sessions on evolving risks, new regulations, and updated procedures are crucial. Make sure both your IT and security teams understand vulnerabilities and best practices. Refresher courses on existing procedures are also valuable. Well-trained staff are better equipped to follow protocols and spot potential issues before they escalate.
Remediation shouldn’t be a one-time fix. Use it as an opportunity to improve your overall control environment. Review your existing processes and identify areas for streamlining or automation. A clearly defined governance structure with documented roles and responsibilities helps ensure accountability and consistency. This also creates a framework for continuous improvement and helps prevent future deficiencies. For more insights on optimizing financial operations, visit the HubiFi blog.
Technology can significantly enhance your remediation efforts. Use tools to centralize the tracking and monitoring of remediation tasks. This provides real-time visibility into progress, allowing you to quickly identify and address any roadblocks. Automated reporting features can also save time and resources, freeing up your team to focus on strategic initiatives. Consider exploring solutions like HubiFi, which offers automated revenue recognition and seamless integrations with your existing systems. You can also schedule a demo to see how HubiFi can help your business.
After remediating existing control deficiencies, your focus should shift to preventing new ones. This proactive approach strengthens your overall control environment and reduces the likelihood of recurring issues. A robust system for preventing future deficiencies involves continuous monitoring, fostering a culture of compliance, and committing to continuous improvement.
Think of your internal controls as a living, breathing system. Regular check-ins and ongoing monitoring are crucial for ensuring they remain effective. This involves tracking key metrics and performance indicators to identify potential weaknesses before they escalate into significant problems. Establish a system for regularly reviewing your controls, perhaps through periodic risk assessments or internal audits. This consistent oversight helps you catch emerging risks and adapt your controls as needed. Measuring the effectiveness of your remediation process is also key. By tracking trends and team performance, you can identify areas for improvement and refine your approach over time. Tools like dashboards and automated reporting can streamline this process and provide valuable insights into your control environment. This data-driven approach allows you to make informed decisions and proactively address potential vulnerabilities. Consider exploring HubiFi's automated solutions for assistance with this.
Compliance isn't just a checklist; it's a mindset. Building a culture of compliance throughout your organization is essential for long-term success. This means clearly communicating expectations, providing adequate training, and empowering employees to take ownership of their roles in maintaining strong internal controls. Collaboration is also key. Engage stakeholders across different departments to ensure everyone understands the importance of compliance and their individual responsibilities. When compliance is embedded in your organizational values, it becomes a natural part of how you do business, reducing the risk of future deficiencies. Effective remediation requires this collaborative effort. Open communication channels and regular feedback loops can further reinforce this culture and encourage continuous improvement. For more insights, check out HubiFi's blog on compliance best practices.
Maintaining strong internal controls requires a commitment to continuous improvement. Regularly review your control framework, looking for opportunities to streamline processes, enhance efficiency, and strengthen oversight. This might involve updating policies and procedures, implementing new technologies, or providing additional training to your team. A robust governance structure is essential for guiding these efforts. Clearly defined roles, responsibilities, and decision-making processes ensure everyone is on the same page and working toward the same goals. By proactively identifying and addressing control gaps, you create a more resilient and adaptable organization, better equipped to handle future challenges. Embrace a mindset of continuous learning and improvement, and your control environment will evolve and strengthen over time. Remember, strong internal controls are not a destination but an ongoing journey. Schedule a demo with HubiFi to discuss how we can help you achieve this.
After putting in the work to remediate control deficiencies, how do you know your efforts are actually working? Measuring your success is crucial. It helps demonstrate the value of your compliance program, justify resource allocation, and continuously improve your internal controls. This involves tracking key performance indicators (KPIs) that align with your remediation goals.
Start by defining specific, measurable, achievable, relevant, and time-bound (SMART) metrics. These KPIs should directly reflect the effectiveness of your remediation efforts. For example, if you're addressing a deficiency in your invoice approval process, a relevant KPI might be the reduction in the number of invoices paid without proper authorization. Choosing the right KPIs provides a clear picture of your progress and helps you identify areas for further improvement. For more guidance on setting effective goals, check out this article on SMART goals.
One essential KPI is your control effectiveness rate. This metric measures the percentage of critical controls tested that are operating effectively. A higher control effectiveness rate indicates a stronger internal control system and a reduced risk of future deficiencies. Regularly assessing your control effectiveness helps maintain a robust compliance posture and quickly identify any emerging weaknesses. Resources like this article on measuring governance, risk, and compliance offer further insights into control effectiveness.
How quickly you can remediate identified deficiencies is another important factor. Tracking your remediation time, from identification to implementation of corrective actions, helps you understand the efficiency of your remediation process. Shorter remediation times demonstrate a proactive approach to compliance and minimize the potential impact of control weaknesses. This resource on testing and monitoring controls offers helpful information on streamlining your remediation process.
Finally, consider the broader, long-term impact of your remediation efforts. Effective remediation goes beyond simply fixing immediate problems; it fosters a culture of compliance throughout the company. This includes engaging stakeholders across different departments, providing training to staff, and embedding compliance into everyday operations. By creating a culture of compliance, you reduce the likelihood of future deficiencies and build a stronger, more resilient organization. For more information on building a strong compliance culture, explore this article on compliance gaps and remediation techniques.
Automating parts of your control deficiency remediation process can save your team time and resources. Let's explore the advantages of automation and how HubiFi can help.
Think of automation as your secret weapon for more efficient and effective control deficiency remediation. By integrating technology, you can streamline processes and reduce manual work, freeing up your team to focus on higher-level tasks. This increased efficiency translates to faster identification and remediation of control deficiencies, minimizing their potential impact. As ISACA points out, automation improves the efficiency of control execution, even if it can't fix underlying issues with your risk management framework. Beyond efficiency, automation gives you a clearer picture of your operations. With the ability to analyze large datasets in real time, you can quickly pinpoint areas needing remediation, allowing for proactive intervention. For a deeper dive into the benefits of automating internal controls, check out this resource from Diligent. Finally, automated controls play a crucial role in maintaining compliance with industry regulations and standards. They help safeguard your data and ensure adherence to relevant rules, a point emphasized by SafePaaS. This is especially critical in today's increasingly regulated business environment.
HubiFi takes a comprehensive approach to automation, using advanced technology to enhance control deficiency remediation. Our automated workflows ensure that control deficiencies are identified and addressed quickly, reducing the time and resources typically required for manual remediation. This streamlined process not only saves you time but also aligns with best practices in risk management and compliance. By incorporating automation into our internal control framework, we enable continuous monitoring and real-time reporting—essential for maintaining effective controls. This approach allows businesses to adapt quickly to changing risks, much like the SOX testing automation discussed by Workiva. HubiFi’s solutions give you better visibility and control over your financial processes, helping you stay ahead of potential issues and maintain a strong compliance posture. Learn more about our pricing or schedule a demo to see how HubiFi can transform your control deficiency remediation process.
What's the difference between a design deficiency and an operational deficiency?
A design deficiency means the control itself is flawed or missing altogether, like a ship with a hole in its hull. An operational deficiency means the control exists but isn't being used properly, like having a life jacket but not wearing it.
How can I get my team on board with remediation efforts?
Explain why these changes are important, not just what they are. Involve your team in the process so they feel invested. Provide training and support so everyone feels confident in the new procedures. Open communication is key.
Our systems are so complex, how can we even begin to identify control deficiencies?
Start by breaking down your processes into smaller, manageable chunks. Talk to the people involved in each step to understand where things might be going wrong. Look for patterns in errors or inconsistencies. Don't be afraid to bring in outside expertise if you need a fresh perspective.
We're short on resources, how can we prioritize remediation efforts?
Focus on the deficiencies that pose the biggest risks to your business. What could cause the most financial or reputational damage? Address those first. Also, consider using technology to automate some aspects of remediation, which can free up your team's time.
How can we prevent control deficiencies from happening in the first place?
Regular monitoring is key. Think of it like regular health checkups for your business. Also, foster a culture of compliance where everyone understands the importance of strong controls. And finally, always be looking for ways to improve your processes. A commitment to continuous improvement is the best defense against future deficiencies.
Former Root, EVP of Finance/Data at multiple FinTech startups
Jason Kyle Berwanger: An accomplished two-time entrepreneur, polyglot in finance, data & tech with 15 years of expertise. Builder, practitioner, leader—pioneering multiple ERP implementations and data solutions. Catalyst behind a 6% gross margin improvement with a sub-90-day IPO at Root insurance, powered by his vision & platform. Having held virtually every role from accountant to finance systems to finance exec, he brings a rare and noteworthy perspective in rethinking the finance tooling landscape.